In this article, we will explore the evolution, types, benefits, and applications of digital twins. We will also examine a real case led by VASS in an energy plant.
Keep reading to discover how this technology is transforming the way companies manage and optimize their operations.
Digital twins are a key tool in Industry 4.0. This technology allows for the efficient management of complex assets and systems. Through these virtual models, entities, processes, or physical systems are replicated in real-time. This provides a comprehensive and precise view for informed decision-making.
Although their origin dates back to the 1960s, it is with Industry 4.0 that they have become popular. Thanks to the integration of sensors, Big Data, and predictive analysis, digital twins offer impressive accuracy. This makes them a fundamental piece for optimizing operations and improving productivity.
There are two main types: product twins and process twins, which we will discuss further. Both enable simulations, analysis, and continuous improvements in asset management. The benefits range from cost reduction to better quality and sustainability.
In this article, we will explore the evolution, types, benefits, and applications of digital twins. We will also examine a real case led by VASS in an energy plant.
Keep reading to discover how this technology is transforming the way companies manage and optimize their operations.
History and Evolution of Digital Twins
The history of digital twins dates back to the 1960s. At that time, unique applications were used to replicate limited aspects of physical systems, mainly for experimental studies. During the 1980s, simulation became a standard tool, facilitating the analysis of complex systems, although still in a disconnected manner without real-time integration.
With the turn of the millennium, multilevel systems emerged. These allowed for greater complexity in the virtual representation of processes and products. However, it was from 2015 onwards, with the advent of Industry 4.0, that digital twins reached their full potential.
The integration of advanced technologies such as the Internet of Things (IoT), Big Data, and real-time analysis has been key to this evolution. Today, digital twins not only replicate physical systems but also predict future behaviours. This is possible thanks to connectivity and real-time data analysis.
In short, the evolution of digital twins has been a continuous and unstoppable process. From simple simulations in the 1960s to the complex predictive models of today, this technology has transformed asset management and optimization across multiple industries
What Are Digital Twins?
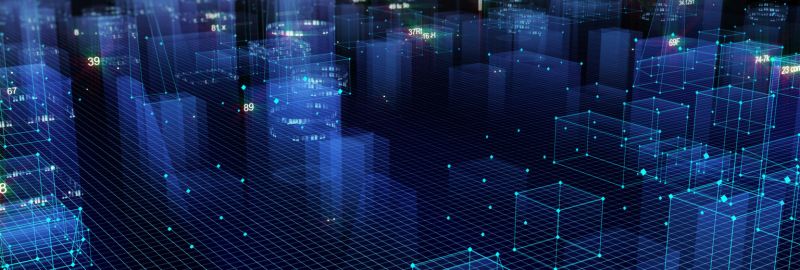
Digital twins are virtual representations of entities, processes, or physical systems that are synchronized in real-time. Their main function is to accurately reflect the current state of their physical counterparts, enabling deep analysis and data-driven decision-making.
Unlike other models, digital twins do not simply replicate the appearance or static behaviour of an object; they evolve along with their physical counterpart, capturing changes and dynamics as they occur.
It is important not to confuse digital twins with other concepts such as simulation, 3D models, or telemetry.
A simulation is a specific process that imitates a particular scenario, while a digital twin is a dynamic and continuous model that reflects the real state at all times.
On the other hand, a 3D model only provides a static visual representation of an object, without incorporating operational data or interacting in real-time.
Lastly, telemetry, although it captures real-time data, lacks the ability to integrate and visualize this data comprehensively and contextually as a digital twin does.
In summary, digital twins not only replicate but also evolve, providing a comprehensive and real-time view that goes beyond other seemingly similar concepts.
Types of Digital Twins
There are mainly two types of digital twins: product or equipment twins and process or operations twins.
Each has its own focus and applications, but both share the goal of improving efficiency and performance through real-time synchronization with their physical counterpart.
Product or Equipment Twins
A product or equipment twin replicates a specific physical object, such as a machine, vehicle, or any other equipment. Its primary purpose is to foresee potential issues before they occur and optimize the product's performance and quality.
For example, a digital twin of a wind turbine can simulate different weather conditions to identify possible failures and adjust parameters to maximize efficiency.
By conducting virtual tests on a digital twin, costly errors in the physical world can be avoided, thereby improving reliability and reducing downtime.
Process or Operations Twins
Process or operations twins, also known as digital twins of an organization (DTO), focus on complete processes within an organization, such as production, supply chain, or resource management. Process twins allow for the modeling and analysis of workflows, identification of bottlenecks, and optimization of planning and execution.
For instance, a digital twin of a manufacturing plant can simulate different production configurations to maximize efficiency or minimize waste.
By monitoring and adjusting processes in real-time, companies can quickly respond to changes in demand, resolve issues before they affect production, and improve the overall quality of the product.
Moreover, these digital twins help organizations predict the impact of new policies or operational changes, making strategic decision-making easier.
Both product twins and process twins are powerful tools for enhancing efficiency, reducing costs, and optimizing performance across various industries.
While the former focuses on the maintenance and optimization of specific equipment, the latter provides a comprehensive view of organizational processes, enabling continuous improvement and greater adaptability.
Benefits of Digital Twins
Digital twins offer a wide range of benefits that directly impact the efficiency, productivity, and profitability of companies. Among them:
Improved Productivity: Digital twins allow for the optimization of processes and operations by providing a clear and real-time view of physical systems. This facilitates the identification of inefficiencies and the implementation of continuous improvements.
Reduced Downtime: By predicting potential failures and enabling predictive maintenance, digital twins minimize the downtime of machines and equipment. This results in longer operating times and reduced economic losses.
Supply Chain Optimization: By offering a comprehensive and detailed view of each stage of the process, digital twins enable better inventory management, logistics optimization, and reduced delivery times.
Improved Quality: Through continuous simulations and analyses, digital twins help detect and correct quality issues before they become costly failures. This ensures more reliable final products with fewer defects.
Business Model Innovation: Digital twins enable the monetization of data and digital services, opening new business opportunities and revenue streams, such as subscription-based services or proactive maintenance.
Enhanced Decision-Making: By integrating predictive analysis and simulations, digital twins provide valuable information for strategic decision-making. Companies can evaluate different scenarios and make decisions based on precise and up-to-date data.
Greater Sustainability: Digital twins contribute to reducing resource waste, improving energy efficiency, and optimizing material use, thereby supporting sustainability and environmental responsibility goals.
Real-Time Regulatory Compliance: Digital twins allow for real-time monitoring of compliance with health, safety, and environmental regulations, ensuring that operations meet required standards without interruptions.
Together, these benefits make digital twins an essential tool for companies looking to remain competitive, innovative, and sustainable in an ever-evolving industrial environment.
Applications and Use Cases
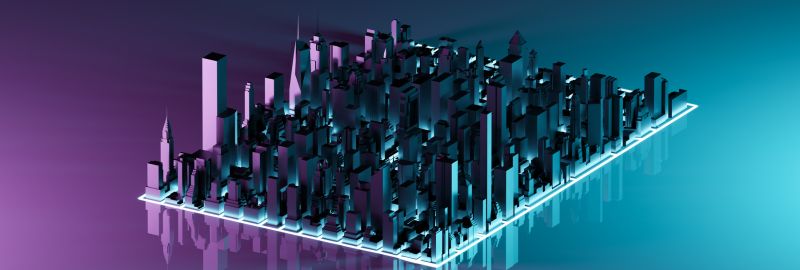
Digital twins have applications in a wide variety of sectors, each leveraging their capabilities to optimize operations, improve quality, and reduce costs. Some of the most relevant applications are:
Manufacturing: In the manufacturing industry, digital twins are used to simulate and optimize production processes. They allow for the prediction of problems, adjustment of machinery configurations, and improvement of production line efficiency. Additionally, they help reduce downtime through predictive maintenance.
Healthcare: In the healthcare sector, digital twins can model the human body or specific medical systems to personalize treatments and predict outcomes. For example, surgical procedures can be simulated to plan complex operations or improve medical devices before their application on patients.
Disaster Management: Digital twins are employed to simulate disaster scenarios and plan effective responses. They can model a city's infrastructure to predict the impact of an earthquake, flood, or other natural disaster, allowing for better preparation and a faster response.
Product Development and Customization: Digital twins enable companies to design and test products in a virtual environment before manufacturing. This reduces development cycles and allows for adjustments on the fly. They also facilitate the customization of products according to the specific preferences and needs of customers.
Smart Cities: Smart cities use digital twins to manage and optimize public services such as energy supply, traffic management, and waste collection. By integrating real-time data, cities can improve operational efficiency, reduce energy consumption, and provide a safer and more comfortable environment for citizens.
Supply Chain Logistics: Digital twins allow for more efficient supply chain management by providing real-time visibility of all aspects, from inventory to product delivery. This helps optimize routes, improve planning, and reduce operational costs.
Power Plants: In the energy sector, digital twins are used to replicate power plants and optimize their operation. They enable the efficient management of resources, the integration of renewable energies, and the continuous improvement of safety and operational efficiency.
Case Study: Implementation of Digital Twins in an Energy Plan
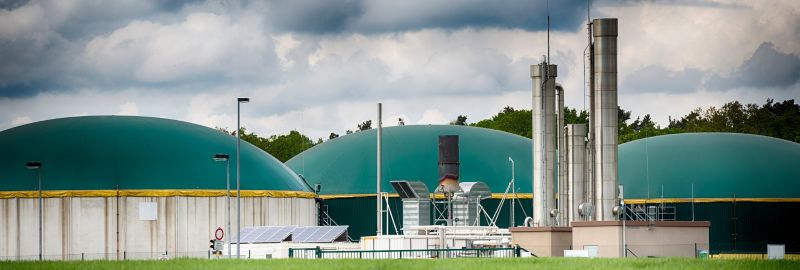
A notable example of the implementation of digital twins is found in the energy sector, specifically in an energy plant with a project led by VASS. This real case illustrates how digital twins can optimize the operation and maintenance of critical facilities.
Phase 1: The Platform
The first phase involved creating a digital replica of the energy plant using photogrammetry. This process automated the digital representation of the plant and integrated the information into a centralized system.
The data was stored in the cloud, allowing quick and easy access from mobile devices, tablets, PCs, or even 3D glasses.
This accessibility improved the ability to resolve issues remotely, reducing intervention times and minimizing operational downtime.
Phase 2: Data Integration
In the second phase, real-time data was integrated with various plant systems, including SCADA, CMMS, sensors, and energy control systems.
This integration enabled continuous monitoring of equipment and process performance, providing a solid foundation for operational decision-making.
Phase 3: State Comparison
One of the key features of the digital twin was the ability to compare the current state of the plant with its future projections. Using cameras, images were captured at different times to visualize the progress of the works and compare them with the initial plans.
This tool allowed for accurate certification of the works and rigorous progress tracking.
Phase 4: Proactive Maintenance
The digital twin was integrated with the plant's maintenance systems, such as SAP PM and SAP Asset Manager. This allowed for efficient management of equipment maintenance, physical locations, and work orders.
The integration facilitated proactive management, reducing breakdowns and optimizing available resources.
Phase 5: Simulation and Predictive Analysis
In the final phase, an interactive dashboard was implemented that allowed for “what-if” simulations.
Users could adjust variables such as personnel levels or production speed and observe how these changes impacted the plant's KPIs. This was achieved using interpolation and regression algorithms, providing predictive analysis that helped improve planning and efficiency.
This case demonstrates how digital twins can transform the operation of an energy plant. From maintenance optimization to scenario simulation, this technology has enabled VASS to improve efficiency, reduce costs, and ensure more sustainable and safer plant operations.