The demands for faster, more reliable deliveries are higher than ever, and industries are under pressure to ensure seamless operations and customer satisfaction. Smart packaging meets these demands by offering accurate, up-to-the-minute data on products as they move through each stage of production and delivery.
Smart packaging is transforming how industries manage and deliver products. It combines advanced technologies like RFID (Radio Frequency Identification) with real-time data systems to streamline processes, reduce errors, and improve efficiency throughout the supply chain.
Unlike traditional packaging methods, smart packaging can capture and share valuable information automatically, minimizing manual tasks and the risk of human error.
The demands for faster, more reliable deliveries are higher than ever, and industries are under pressure to ensure seamless operations and customer satisfaction. Smart packaging meets these demands by offering accurate, up-to-the-minute data on products as they move through each stage of production and delivery.
Additionally, smart packaging brings significant environmental benefits. By reducing errors and improving efficiency, it cuts down on wasted materials and unnecessary shipments, resulting in a smaller carbon footprint. This is increasingly essential as businesses and consumers alike prioritize sustainability.
In this article, we explore the core technologies behind smart packaging, how it optimizes processes from inventory management to product tracking, and the future possibilities it brings to the field of product delivery. Whether improving logistics, reducing costs, or supporting environmental goals, smart packaging is set to play a vital role in the evolution of product delivery.
Key Technologies in Smart Packaging
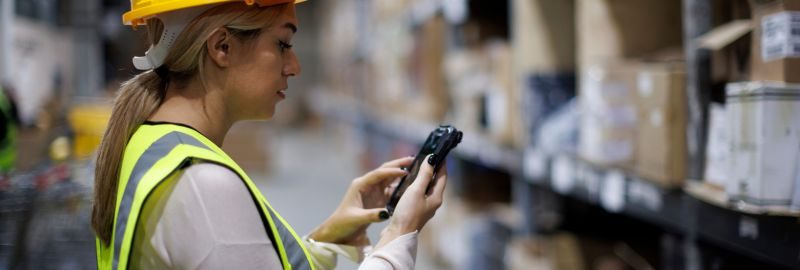
At the heart of smart packaging are cutting-edge technologies that provide enhanced visibility and control over products throughout the supply chain.
One of the primary tools is RFID (Radio Frequency Identification), which enables automated data capture and tracking without needing direct line-of-sight, unlike traditional barcodes. With RFID, each item can carry a unique identifier, allowing it to be tracked from production through delivery, providing real-time data that improves efficiency and accuracy.
Unlike traditional barcodes that require manual scanning and are limited in the information they can store, RFID tags hold and transmit detailed data automatically. This automation reduces labour costs and minimizes errors associated with manual entry. Additionally, RFID technology supports faster, multiple-item scanning, saving valuable time in warehouses and distribution centers.
Another essential element in smart packaging is the integration of data systems like SAP. By connecting RFID data with SAP, businesses can have a centralized view of their inventory and shipments, making it easier to manage stock, prevent losses, and improve response times. This integration enables companies to address customer needs more effectively, offering higher accuracy in orders and minimizing delays.
Together, RFID and data systems like SAP make smart packaging a powerful solution, streamlining the entire logistics process and setting new standards for product tracking and delivery reliability.
Phases of the Smart Packaging Process
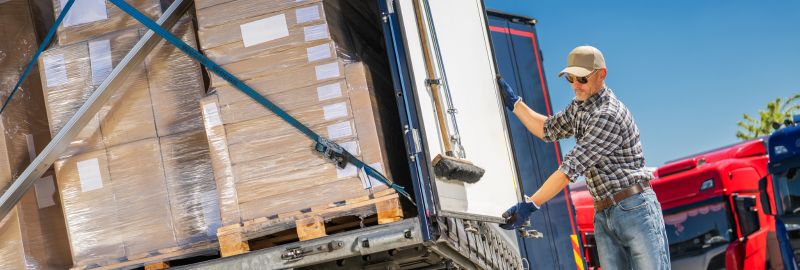
The smart packaging process leverages advanced technology to streamline each stage of product handling and delivery, transforming traditional workflows into efficient, data-driven operations.
Smart packaging begins the moment an order is placed and follows each item through production, packaging, and shipment. This process is designed to ensure that the correct products reach the right customers in the best possible condition.
The smart packaging process is divided into key phases that specifically address common challenges in product delivery—from minimizing errors to optimizing production efficiency. Let’s take a closer look at these phases.
Phase 1: Load Control and Error Reduction
The first phase of smart packaging, Load Control and Error Reduction, is centered on minimizing mistakes during the initial stages of packaging and shipping. This phase begins when the order is placed, and the system collects all relevant information, such as product type, quantity, and any unique specifications.
To facilitate this process, RFID tags are generated with critical order data and attached to each package. These tags contain sales, manufacturing, and customer-specific information, ensuring that each item is accurately identified and tracked throughout the loading process.
As packages reach the dispatch area, RFID readers scan the tags and verify that all products align with the order requirements. This automatic verification step provides a robust quality check, catching any inconsistencies or missing items before they are shipped.
For example, if a customer orders 20 custom-colored chairs, the system generates 10 packages with two chairs per package, each bearing an RFID tag with precise details. As each box passes through RFID readers, the system counts and validates the packages, checking them against the order. If everything is correct, the process continues smoothly; if a discrepancy is detected, the system flags it and halts the process until the issue is resolved.
Benefits of Phase 1
- Error Reduction: By using RFID tags and automated readers, loading errors are drastically reduced. This minimizes the chances of incorrect or incomplete orders, enhancing customer satisfaction.
- Time Optimization: Error reduction also shortens loading times, as there are fewer interruptions due to manual checks or error corrections.
- Increased Production Capacity: Faster, more reliable loading processes mean production can scale efficiently without sacrificing quality.
- Employee Satisfaction: With RFID handling much of the verification, employees can focus on value-added tasks rather than repetitive data entry and checks.
Through these measures, Phase 1 establishes a foundation of accuracy and efficiency, ensuring that orders are correctly packed and verified before moving on to the next steps in the smart packaging process.
Phase 2: From Data to Efficiency
In Phase 2: From Data to Efficiency, smart packaging systems focus on harnessing data to streamline the entire production and delivery process. While Phase 1 aims to reduce errors, Phase 2 emphasizes real-time data capture and analysis, transforming raw information into actionable insights that boost efficiency at every stage.
Without Data Measurement: In traditional production lines, workers manually report each stage of the process, which is time-consuming and prone to delays. This manual method can slow down responses to customer needs, as there’s limited visibility into real-time progress and status. Without automation, inefficiencies add up, creating bottlenecks that affect flexibility and overall operational flow.
With Data Measurement: Smart packaging leverages RFID technology to capture data seamlessly as products move along the supply chain. From the raw materials stage, each item is assigned a unique RFID tag that is read by RFID scanners at each checkpoint. This system automatically records the progress of materials and time taken at each step, generating a clear and detailed overview of production and logistics.
Data measurement not only provides an invaluable view of efficiency but also enables immediate problem-solving. If an issue arises, such as a delay or product discrepancy, the system can alert teams in real-time, allowing them to resolve it quickly before it affects delivery schedules.
Additionally, it enables enhanced management capabilities, including tracking returns and handling repairs with minimal disruption.
Benefits of Phase 2:
- Productivity Improvement: By predicting and preventing downtime, data measurement helps optimize production line efficiency, reducing overall manufacturing time.
- Increased Sales and Reduced Operational Costs: Real-time quality control prevents extra costs due to unplanned downtime, helping to increase sales through reliable delivery times.
- Enhanced Decision-Making: With real-time data analytics, companies can respond flexibly to challenges, implementing solutions instantly and maintaining smooth operations.
- Improved Reputation and Quality: Real-time quality checks reduce or even eliminate returns, ensuring products consistently meet customer expectations and enhancing brand reputation.
Phase 2 solidifies the smart packaging process by ensuring that data is used effectively, allowing companies to operate with high efficiency, prevent errors, and provide an improved customer experience from production to delivery.
Smart Packaging and Inventory Control
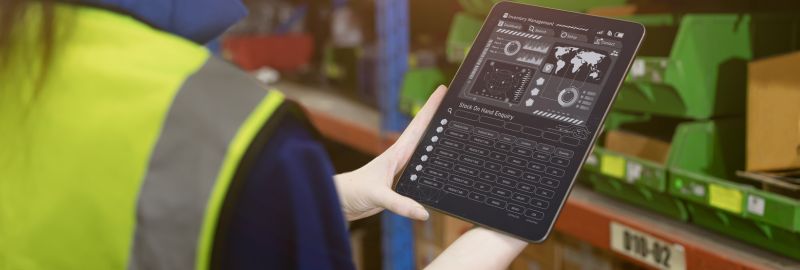
An essential aspect of smart packaging is its ability to transform inventory management through automation and real-time visibility. Traditional inventory management methods often rely on manual counting and barcodes, which can be slow and error-prone. In contrast, smart packaging utilizes RFID technology to streamline and automate these processes, significantly enhancing accuracy and speed.
Real-Time Inventory Tracking
With RFID, inventory can be tracked in real time. Fixed-point RFID readers scan tagged items as they move through the supply chain, updating inventory records without any manual intervention.
This automation allows companies to conduct inventory counts in a fraction of the time it would normally take, reducing labour costs and minimizing the risk of human error.
Enhanced Accuracy and Reduced Hidden Inventory
Smart packaging systems can prevent hidden inventory by accurately tracking every item’s location within the warehouse. RFID tags allow each product to be uniquely identified, enabling quick stock checks and immediate visibility into deviations from expected inventory levels.
This not only improves accuracy but also ensures that products are easy to locate, reducing the time employees spend searching for items and ultimately improving customer fulfilment rates.
Theft Prevention and Stock Deviation Detection
Real-time tracking also supports theft prevention and immediate alerts for any deviations in stock levels.
RFID’s detailed data logs allow for precise monitoring of inputs and outputs, enabling the system to detect any inconsistencies quickly. This can reduce loss due to theft, enhance security, and ensure more accurate inventory counts over time.
Benefits of Smart Inventory Control
- Time Efficiency: Inventory counts that previously took hours or days can now be completed in minutes using handheld RFID devices.
- Elimination of Human Error: Automated data capture drastically reduces mistakes commonly associated with manual inventory checks.
- Increased Productivity: Faster inventory management frees up employees to focus on higher-value tasks, optimizing workforce productivity.
- Prevention of Stock Shortages: By detecting stock deviations early, smart inventory control minimizes the risk of shortages and delays in the supply chain.
Smart packaging offers an efficient, automated approach to inventory control that minimizes errors, prevents stock loss, and ensures optimal inventory levels are maintained, setting a new standard in product delivery and management.
Benefits of Implementing Smart Packaging
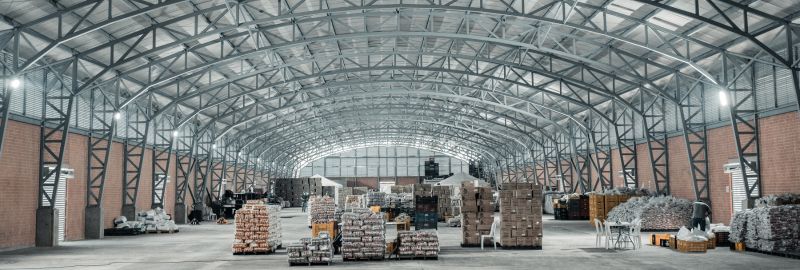
Smart packaging provides a range of benefits that go beyond improving logistics and inventory. By integrating advanced technology like RFID and data analytics, companies can achieve higher levels of productivity, accuracy, and customer satisfaction, all while reducing operational costs and enhancing sustainability.
For a deeper understanding of how AI is transforming warehouse logistics, explore our insights on Artificial Intelligence in Warehouses.
1. Productivity Improvement
With automated data capture and tracking, smart packaging reduces the time spent on manual tasks. Employees no longer need to conduct time-consuming checks or reporting, allowing production lines to move faster and with fewer interruptions.
This increased efficiency leads to higher production output without sacrificing quality, making it possible for companies to meet growing customer demands with ease.
2. Increased Sales and Reduced Operational Costs
Real-time quality control and error reduction minimize costly mistakes that can disrupt production and delay deliveries. With smart packaging, companies can streamline processes, lowering operational costs while ensuring products reach customers on time.
This reliability in delivery leads to greater customer trust and, ultimately, increased sales. By reducing unnecessary delays and maintaining product quality, smart packaging helps protect a company’s bottom line.
3. Enhanced Decision-Making
Smart packaging provides data-driven insights that support better decision-making. Through data analytics, companies can monitor and adjust processes in real time, responding swiftly to any issues and identifying areas for further improvement.
This agility allows businesses to be more flexible and proactive, making decisions that keep operations smooth and efficient.
4. Improved Reputation and Quality
Consistent, high-quality products are crucial for a strong brand reputation. Smart packaging supports real-time quality control, catching potential issues before products leave the warehouse. This significantly reduces the chances of returns due to errors, leading to better customer satisfaction and trust.
A reputation for quality can also provide a competitive edge in the market, helping companies retain loyal customers and attract new ones.
5. Environmental Sustainability
By optimizing processes and reducing errors, smart packaging cuts down on waste and unnecessary shipments. This helps companies minimize their environmental footprint, aligning with growing consumer demand for eco-friendly practices.
Less waste and fewer resources spent on rework or replacement orders contribute to a greener, more sustainable operation.
In summary, implementing smart packaging provides companies with a competitive advantage through improved productivity, cost savings, and customer satisfaction, while supporting long-term sustainability goals. It’s a comprehensive solution that addresses today’s complex demands in product delivery and management.
Integrating SAP and RFID: The Core of Smart Packaging
One of the most powerful aspects of smart packaging is the seamless integration of RFID technology with enterprise systems like SAP. This integration allows companies to manage
logistics and resources with high precision, creating an automated and flexible approach to product delivery that adapts to changing business needs.
How SAP and RFID Work Together
SAP is a widely used enterprise resource planning (ERP) platform that helps companies centralize and manage critical data across departments. When combined with RFID, SAP can automatically capture and analyze real-time information on inventory, production, and shipping, eliminating manual data entry and reducing the chances of errors.
RFID tags, which uniquely identify each item in the supply chain, continuously send data to SAP systems, providing a complete and up-to-date view of product status and location.
A Modular and Scalable Solution
The integration of SAP and RFID is highly modular and scalable, meaning it can be customized and expanded as a company’s needs evolve. This flexibility is key in today’s fast-paced market, where changes in demand, product specifications, or logistical requirements can occur frequently.
Companies can tailor the integration to support specific processes, whether it’s inventory control, order verification, or tracking returns, ensuring the system aligns perfectly with business objectives.
Automating Business Logistics with RFID
By using RFID-enabled smart packaging within an SAP framework, companies can automate their logistics flows from start to finish.
For example, as items move through different points in the supply chain, RFID readers track their progress and update SAP in real time. This continuous communication ensures that stock levels are accurate, orders are fulfilled correctly, and any discrepancies are flagged immediately.
Benefits of Integrating SAP and RFID:
- Streamlined Operations: Real-time data updates create a smooth, automated logistics flow, helping teams to manage and track resources without interruption.
- Improved Accuracy and Efficiency: Automated data capture reduces human errors, while SAP’s centralized data view supports quick and informed decision-making.li
- Increased Adaptability: The modular nature of SAP and RFID integration allows companies to scale or modify operations as they grow, remaining agile and responsive to new challenges.
- Enhanced Customer Satisfaction: By improving order accuracy and reducing delivery times, companies can ensure a better customer experience, reinforcing brand loyalty.
Through the integration of SAP and RFID, smart packaging becomes an essential tool in creating a connected, data-driven supply chain that meets the highest standards in efficiency, accuracy, and adaptability.
Smart packaging is revolutionizing the future of product delivery, enabling businesses to achieve unprecedented levels of efficiency, accuracy, and customer satisfaction through advanced technologies like RFID and SAP integration. As demand for reliable, data-driven
solutions grows, companies need experienced partners who understand the intricacies of these systems and can tailor them to specific needs.
At VASS, we are experts in designing and implementing smart packaging solutions that optimize logistics and elevate operational performance. Our team brings deep technical expertise and a commitment to innovation, helping businesses unlock the full potential of smart packaging to stay ahead in a competitive market.